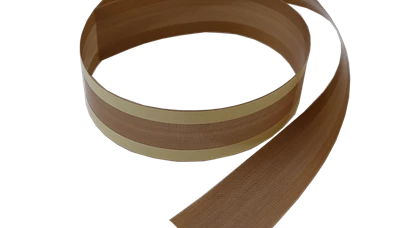
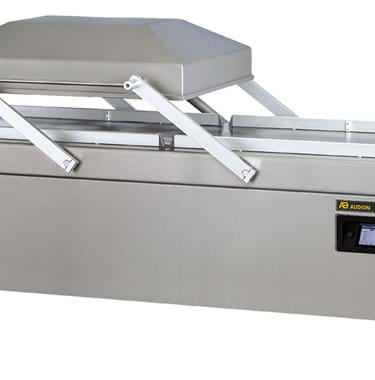
Produkte
Validierbare Audionvac VMS 503
Validierbare Doppelkammer-Vakuummaschine im XL-Format, die qualitativ hochwertige Schweißnähte, Komfort ein zuverlässig stabiles Vakuum bietet.
Haben Sie Interesse an unserer VMS 503?
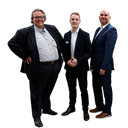
Gerne unterstützen wir Sie bei Ihrer Anfrage oder führen eine Demo mit Ihrem Produkt durch.
Entwickelt, um höchsten Qualitätsansprüchen zu genügen
Die validierbare Audionvac VMS 503 ist eine extra große Doppelkammermaschine aus der Familie der validierbaren Audionvac-Schweißgeräte. Dieses Standmodell ist mit zwei leicht zu reinigenden Vakuumkammern mit flachem Boden ausgestattet. Der hohe Schwingdeckel aus rostfreiem Edelstahl und zwei Paar doppelter Schweißbalken ermöglichen es Ihnen, innerhalb eines Zyklus mehrere oder besonders große Produkte zu verpacken und dadurch Ihre Effizienz und Ihren Output zu erhöhen.
Die Audion Touch Techware mit dem integrierten Temperaturkontrollsystem (ATC) bietet Ihnen die volle Kontrolle über alle Prozessparameter, d.h. über den Vakuum- und Gasdruck sowie die Schweißtemperatur und -zeit und den Schweißdruck. Sollten sich die Parameter außerhalb des Toleranzbereiches befinden, wird über die Alarmfunktion ein Alarm ausgelöst und die Maschine automatisch gestoppt. Alle kritischen Schweißparameter können exportiert und für eine spätere Auswertung extern auf einem USB-Stick gespeichert werden.
Über einen Sensor werden der Vakuum- und Gasdruck überwacht und kontrolliert, um zu gewährleisten, dass die voreingestellte Vakuumhöhe nach jedem Zyklus erreicht wird, damit die Qualität und Sicherheit Ihrer Produkte nicht beeinträchtigt wird.
Die bi-aktiven Schweißbalken erzeugen unter hohem Druck eine 8 mm breite hermetische Schweißnaht die eine optimale Zuverlässigkeit in anspruchsvollen Industrien gewährleistet.
Die validierbare VMS 503 entspricht den Vorgaben der ISO-Richtlinie 11607-2 und kommt in der Industrie, High-Tech-, Pharma- und Medizinbranche zum Einsatz, u.a. beim Verpacken medizinischer Instrumente.
Alle Vorteile auf einen Blick:
-
- Doppelkammer-Lösung für eine optimierte Effizienz und maximalen Durchsatz
- Zwei Paar bi-aktive 8 mm breite Impuls-Schweißbalken
- Schweißparameter einfach anpassen, damit ein konstant hohes Vakuum und zuverlässige Schweißnähte für exzellente Ergebnisse erzeugt werden.
- Zwei leicht zu reinigende Vakuumkammern aus rostfreiem Edelstahl mit hohem Schwingdeckel für größere Chargen oder Produkte
- Benutzerfreundlicher Touchscreen (ADC). Bis zu 50 Schweißprogramme können gespeichert und Daten exportiert und auf einem USB Stick gespeichert werden.
- Alarmfunktion und automatischer Stopp bei Schweißparametern außerhalb des Toleranzbereichs.
- Verschiedene konfigurierbare Optionen und Zubehör erhältlich
- Entspricht den Anforderungen an validierbares Verschweißen gemäß ISO 11607-2
Das macht unsere Maschine einzigartig
Wir bieten Ihnen qualitativ hochwertige Verpackungsmaschinen, damit Ihr Unternehmen weiter wachsen kann.
Output erhöhen
Dank der Doppelkammern mit flachem Boden und dem hohen Schwingdeckel können Sie innerhalb eines Zyklus mehrere oder besonders große Produkte verpacken. Wenn Sie die eine Kammer vorbereiten, während die andere Kammer gerade zum Verschweißen genutzt wird, können Sie im Vergleich zu einer Audionvac Einkammer-Vakuummaschine doppelt schnell arbeiten. Der Schwingdeckel ist einfach zu bedienen und ermöglicht das Verschweißen mittlerer bis großer Chargen. Damit Sie die VMS 503 reibungslos in Ihren Verpackungsprozess integrieren können und Ihre Verpackungen garantiert den erforderlichen Qualitätsstandards entsprechen, bietet Audion eine große Auswahl an Optionen und Zubehör.
Benutzerfreundlicher Touchscreen
Der benutzerfreundlicher Touchscreen mit der integrierten Audion Touch Techware kann bis zu 50 verschiedene Programme speichern. So finden Sie für jedes Ihrer Produkte das passende Programm und die passenden Prozessparameter. Sie haben also jederzeit das passende Programm zur Verfügung, um Arbeitsabläufe zu optimieren und Fehlern in den Produktionsabläufen vorzubeugen. Sie können schnell und einfach zwischen Chargen wechseln, Ihre Produktion genauestens kontrollieren und Ihre Effizienz steigern. Auf dem Display werden die Einstellungen und Prozessparameter gut lesbar dargestellt, so dass diese während des Produktionsprozesses schnell und einfach analysiert werden können.
Alarmfunktion
Die Schweißparameter werden über einen Sensor überwacht. Sobald sich eines der Schweißparameter außerhalb des Toleranzbereiches befindet, wird ein Alarm ausgelöst und die Maschine automatisch gestoppt. Der Toleranzbereich kann für jedes der kritischen Prozessparameter individuell festgelegt werden. Diese Funktion trägt aktiv zur Optimierung des Verpackungsprozesses bei, da Fehler vermieden und die Produktionsstandards für das jeweilige Produkt eingehalten werden.
Für Reinräume geeignet
Die validierbare Audionvac VMS 503 kann in sterilen Umgebungen und Reinräumen installiert werden. Voraussetzung hierfür ist, dass die ölbetriebene Pumpe entweder außerhalb des Reinraums untergebracht oder durch eine trockene Vakuumpumpe ersetzt wird. Um die Produktsicherheit noch weiter zu erhöhen, können alle kritischen Prozessparameter exportiert und extern auf einem USB Stick gespeichert werden. Von dort können die Daten dann auf einen PC übertragen und nach verschiedenen Gesichtspunkten ausgewertet werden.
Verifizierung von Prozessparametern
Die VAL VMS 503 von Audion ist eine validierbare Doppel-Vakuumkammer, die regelmäßige Kalibrierungs-, Verifizierungs- und Validierungsdienste erfordert. Audion bietet eine breite Palette von Instrumenten und Lösungen an, die es Unternehmen ermöglicht, die Prozessparameter zu überprüfen.
- Zu den verfügbaren Prüfgeräten gehören:
- ATM (Audion Temperature Meter) für die Messung und Überprüfung der Schweißtemperatur
- ASPM (Audion Seal Pressure Measurement): zur Messung und Überprüfung des durch Druckluft erzeugten Schweißdrucks
- AVLM (Audion Vacuum Level Measurement): zur Messung und Überprüfung des Vakuumdrucks
- Seal Integrity Test (SIT) als Dienstleistung, die eine Dichtheitsprüfung, einen Farb-Eindringtest und einen Peel-Test umfasst.
- Kalibrierservice als Dienstleistung (inklusive Kalibrierzertifikat): Bescheinigung darüber, dass die Prozessparameter der Verpackungsmaschine präzise kalibriert sind.
- IQ/OQ-Prüfung inklusive Zertifikat:
- Abnahmebeurteilung (IQ): Hier wird überprüft, ob die Maschine in einem guten Zustand ist, einwandfrei funktioniert und kalibriert ist.
- Funktionsbeurteilung (OQ): Hier wird die Funktion der Maschine optimiert, damit mit den Materialien der Kunden einwandfreie Schweißnähte erzeugt werden können.
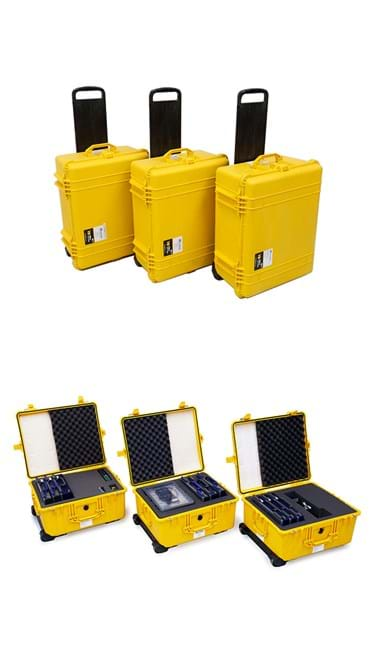
Vorteile
Die Audion VAL VMS 503 bietet Ihnen die folgenden Vorteile:
- Präzise Validierung:
- Mit Hilfe der in der Audion Touch Techware enthaltenen Validierungsfunktion wird die größtmögliche Genauigkeit der Validierung gewährleistet. Über die Validierungsfunktion werden alle kritischen Prozessparameter wie Vakuum- und Gasdruck, Schweißzeit, -druck und -temperatur kontrolliert. Der geringe Toleranzbereich macht die validierbaren Audionvac-Modelle verglichen mit anderen validierbaren Verpackungslösungen konkurrenzlos.
- Höchste Effizienz:
- Die Doppelkammer-Lösung mit zwei Paar Schweißbalken, die dank langsamer Bewegungen wenig Reibung erzeugen und zu einer Optimierung des Durchsatzes beitragen.
- Optimale Hygiene:
- Standardausführung bi-aktive 8 mm breite Impuls-Schweißbalken sowie leicht zu reinigende Vakuumkammern mit flachem Boden.
- Wartungsarm:
- Die Schweißbalken sind zur Reinigung und Wartung einfach herausnehmbar.
- Vakuumkammern:
- leicht zu reinigende Vakuumkammern aus rostfreiem Edelstahl mit flachem Boden und hohem Deckel für mittelgroße und große Verpackungen.
- Alarmfunktion:
- Falls sich eines der Prozessparameter außerhalb des voreingestellten Toleranzbereichs befindet, wird die Maschine sofort gestoppt und ein Alarm ausgelöst.
- 50 Programme speichern:
- Sie können 50 Schweißprogramme speichern und so schnell und einfach das passende Programm für Ihr Produkt auswählen.
- Soft Air-Funktion:
- Kontrollierter Luftstrom für das Verpacken zerbrechlicher oder scharfkantiger Produkte. Die Funktion verhindert, dass das Produkt und/oder die Verpackung beschädigt wird.
- Vakuumpumpe:
- Vakuumpumpe mit einem Volumen von 300 m3/Std für einen schnellen Verpackungszyklus
- Wartungsprogramm:
- Falls die Maschine über einen längeren Zeitraum nicht durgehend in Betrieb ist, erreicht die Vakuumpumpe nicht mehr die ideale Betriebstemperatur. Außerdem enthält die angesaugte Luft Feuchtigkeit, die im Öl zurückbleibt und im Inneren der Pumpe kondensiert, was zu Korrosion führen kann. Über das Kontrollsystem können Sie ein Wartungsprogramm zur Reinigung der Pumpe laufen lassen, damit die Pumpe und das Öl jederzeit einsatzbereit sind.
Optionen
Folgende Optionen sind für die VAL VMS 503 erhältlich:
- (Re-)Kalibrierung:
- Audion bietet einen Kalibrierservice für alle validierbaren Folienschweißgeräte. Die kritischen Prozessparameter (Schweißtemperatur, -stärke, -zeit und -geschwindigkeit) werden mit Messgeräten für unsere Kunden nachvollziehbar aufgezeichnet und auf einem Kalibrierungszertifikat dokumentiert.
- Schwingdeckel einfach öffnen:
- Der Schwingdeckel ist einfach zu öffnen, so dass der Maschinenführer nur wenig Kraft aufwenden muss und ergonomisch arbeiten kann.
- Schweißbalken links-rechts:
- 820 / 820 mm (Standard = vorne-hinten 1080 / 1080 mm)
- Gasspülsystem:
- Dank des Gasspülsystems können Produkte unter Schutzatmosphäre (MAP) verpackt werden. Die Begasung der Produkte mit z.B. Stickstoff verlängert die Haltbarkeit der Produkte oder bietet zusätzlichen Schutz für sehr empfindliche Ersatzteile wie z.B. Platinen.
- Externer Auslass:
- Schließen Sie einen Schlauch an den Auslass der Pumpe an und verhindern Sie so das Entweichen von Partikeln. Dank des Schlauchs können Sie die Maschine in ihrem Gehäuse belassen und dennoch Luft in einen anderen Raum leiten. Dies ist dann von Vorteil, wenn die Maschine in einem Reinraum steht.
- Externe Pumpe:
- Die Vakuumpumpe ist räumlich von der Vakuumkammer getrennt, um zu verhindern, dass über die Vakuumpumpe flüchtige Partikel in die Umgebungsluft entweichen. Die externe Pumpe kommt v.a. in Reinräumen zum Einsatz, wo bereits eine geringe Menge entwichener Partikel die Qualität eines Produktes nachteilig beeinträchtigen können.
- Zugriffsrechte verwalten:
- Verwalten Sie die Zugriffsrechte der einzelnen Mitarbeiter, sowie Passwörter und weitere Login-Daten.
- Flexibler Wechsel:
- Wechseln Sie für maximal 5 Zyklen zwischen Begasung und Vakuum, um den Restsauerstoff so weit wie möglich zu entfernen. Nur möglich in Kombination mit dem Gasspülsystem.
- Strichcodescanner:
- Einfacher Programmwechsel durch Scannen eines Strichcodes.
- Etikettierer:
- Drucken Sie wichtige Daten (z.B. Chargennummern) zur besseren Nachverfolgung auf ein Etikett und kleben Sie dieses auf den Beutel.
- Kontrollgeräte:
- Überprüfen Sie die Qualität der Schweißnähte und die Leistung Ihres Schweißgerätes.
- Bedienfeld verlängerter Arm:
- Ermöglicht eine ergonomische Bedienung der Maschine und erleichtert die Kontrolle der Prozesse.
- Anschlusswerte (wahlweise):
- 200V-3P-50/60Hz | 220V-3P-60Hz
Ersatzteile
Entdecken Sie die verfügbaren Ersatzteile für Ihren VMS 503. Audion Original-Qualität.
- Ersatzteile
- ← Klicken Sie hier, um die benötigten Ersatzteile für Ihren VMS 503 auszuwählen
Kalibrierung/Verifizierung/Validierung
Entdecken Sie die verfügbaren Geräte und Dienstleistungen für Ihr validierbare VMS 503.
- Kalibrierung/Verifizierung/Validierung
- ← Klicken Sie hier für weitere Informationen über unsere Dienstleistungen und Verifizierungsgeräte
Technische Daten
Hier finden Sie die technischen Daten der Audionvac VAL VMS 503:
- Schweißbalken vorne-hinten:
- 1080 / 1080 mm (Standard)
- Schweißbalken links-rechts:
- 820 / 820 mm
- Schweißnahtbreite:
- 8 mm bi-aktiv
- Tatsächliche Größe Vakuumkammern (LxBxH):
- je 730 x 1080 x 280 mm (Standard)
- Kapazität der Pumpe:
- 300 m3/Std.
- Prozessparameter kontrollieren:
- Volle Kontrolle über die Höhe des Vakuums, den Gas- und Schweißdruck sowie die Schweißtemperatur und -zeit.
- Audion Touch Techware:
- Die hochentwickelte Validierungssoftware mit dem integrierten, von Audion entwickelten Temperaturkontrollsystem ATC entspricht den höchsten Anforderungen an validierbares Verpacken.
- 50 Programme speichern:
- Schweißprogramme für kritische Prozessparameter voreinstellen und speichern.
- Zyklus:
- 20 - 45 Sek.
- Material Vakuumkammer:
- Vakuumkammer und Deckel aus rostfreiem Edelstahl
- Gehäuse:
- rostfreier Edelstahl
- Geeignete Folie:
- PA/PE, Vakuumbeutel, Aluminiumbeutel
- Folienstärke:
- 20 - 400 Mikrometer
- Erforderlicher externer Luftdruck:
- 0,3 MPa
- Anschlusswerte:
- 400V-3P-50Hz (Standard)
- Verbrauch:
- 5,5 – 7,8 kW
- Gewicht:
- 775 Kg
- Abmessungen (LxBxH):
- 1213 x 2420 x 1597 mm
Vielfältige Optionen
Passen Sie die VAL VMS 503 Ihren Bedürfnissen an
Dokumentierte Validierung (IQ/OQ)
Ein Team von Experten wird die Abnahme- und Funktionsbeurteilung durchführen. Dazu werden Ihre Maschinen und Beutel verschiedenen Tests unterzogen, um sicherzustellen, dass die Verpackungsmaschine von Audion den erforderlichen Standards entspricht.
Verwaltung der Zugriffsreichte:
Um volle Kontrolle über den Verpackungsprozess auszuüben, können Sie die Zugriffsrechte der einzelnen Maschinenführer auf verschiedenen Ebenen passwortgeschützt verwalten. Dies umfasst die Verwaltung der persönlichen Benutzernamen, der Passwörter und der Zugriffsberechtigungen der einzelnen Maschinenführer.
Etikettierer
Drucken Sie wichtige Informationen wie z.B. Chargennummern und den Namen des Maschinenführers auf ein Etikett und kleben Sie dieses manuell auf den fertig verschweißten Beutel.
Flexibler Wechsel
Wechseln Sie für maximal 5 Zyklen zwischen Begasung und Vakuum, um den Restsauerstoff vor dem Start des Schweißprogramms so weit wie möglich zu entfernen. Dadurch funktioniert das Verpacken unter Schutzatmosphäre (MAP) einwandfrei und Sie erhalten Produkte in Top-Qualität, die absolut sicher verpackt sind.
Pumpe für Reinräume:
Die öl-betriebene Pumpe wird außerhalb des Reinraums platziert, um eine Kontaminierung der sterilen Umgebung im Reinraum zu verhindern. Alternativ kann diese Pumpe, die standerdmäßig enthalten ist, auch durch eine trockene Vakuumpumpe ersetzt werden.
Externer Auslass
Über den externen Auslass kann ein zusätzlicher Schlauch angeschlossen werden, um die verbrauchte Luft außerhalb des Reinraumes auszulassen. Diese Funktion ist für das Arbeiten in steriler Umgebung wie z.B. in Reinräumen in der Medizin- und Pharmabranche geeignet.
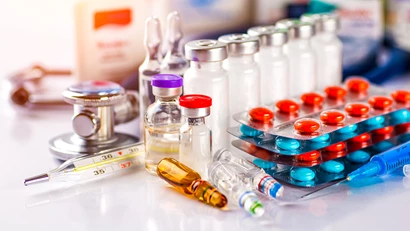
Sprechen Sie uns an
Sie wollen wissen, was die validierbare Audionvac VMS 503 für Ihr Unternehmen bieten kann? Bitte zögern Sie nicht, uns zu kontaktieren, wir freuen uns darauf, gemeinsam herauszufinden, welche Verpackungslösung Ihnen am meisten zugute kommt.
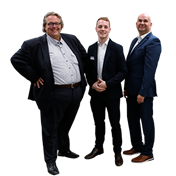
Vertrieb Deutschland
Audion