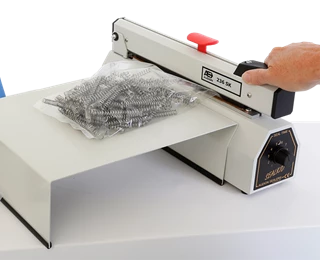
Complete Audion range
With Audion, you have a large choice of high quality packaging machines. This page shows that there’s a solution for every packaging challenge!
Contact us!
If you are looking for a partner who can identify new solutions to your packaging challenge
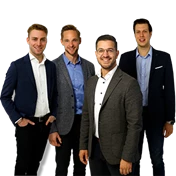
International Sales
Audion